GBG-3210 also uses HSK specifically designed tool holder and direct drive 4/5 axes. It is equipped with high speed spindle, magnetic filter, paper filter system, uses electroforming CBN grinding wheel to provide correction for the deformation after heat treatment to improve gear accuracy and reduce noise. The use of HSK tool holder allows automatic replacement of grinding wheels in different fine and coarse levels, and provides both manufacture efficiency and desired fineness.
The Matrix self-developed intelligent interaction window software can support complete production process, and therefore, without the need of programing training, the user can input parameters and set up production conditions through dialogue procedures to automatically generate NC program, significantly improving work efficiency.
WORKPIECE SPECIFICATIONS | GBC-3210 | GBG-3210 |
---|---|---|
Max. workpiece outside diameter | 100mm | 100mm |
Max. module | M3 | M3 |
MECHANICAL SPECIFICATIONS | ||
Tool/grinding wheel spindle revolutions | 4000rpm | 12000rpm |
Max. slide travel for X-axis | 400mm | 400mm |
Max. slide travel for Y-axis | 350mm | 350mm |
Max. slide travel for Z-axis | 350mm | 350mm |
B- axis tilt range | -100°~100° | -100°~100° |
Smallest tool/wheel diameter | 0.5” | 0.5” |
Largest tool/wheel diameter | 4” | 4” |
Max. load of rotary table (workpiece with fixture) | 50kg | 50kg |
N-axis | Grinding spindle |
---|---|
X-axis | Tool horizontal movement axis |
Y-axis | Tool horizontal movement axis |
Z-axis | Tool vertical movement axis |
B-axis | Workpiece tilt axis |
C-axis | Workpiece rotation axis |
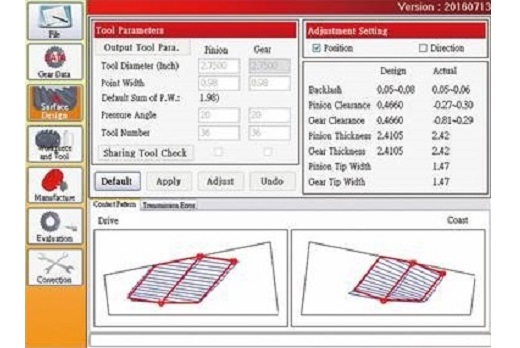
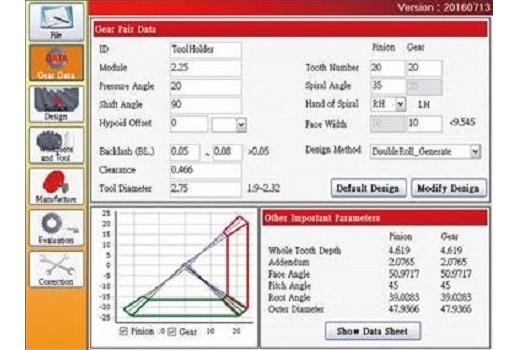
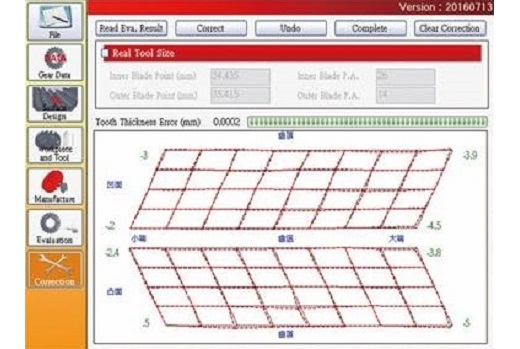
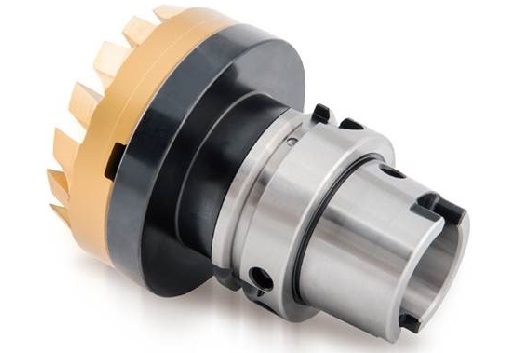