GBC-3210 uses a specific Cup Type Milling Cutter, to manufacture bevel gears in high efficiency. It is further equipped with a specifically designed HSK tool holder that provides flexibility and precision for tool replacement as well as production stability. Besides, B and C axes adopt high-precision direct-drive motor, to increase production precision. There is no need of backlash adjustment problem that happens with a worm gear after wearing, increasing reliability and allowing long-term multi-axis synchronized movement in production. Due to the use of direct-drive motor, there is no backlash problem that happens with worm, allowing accuracy in gear production and eliminating the problem with different precision on left and right flank.
It uses the controller from Intek or world-famous brand Siemens, and is equipped with servo and direct drive motor, and provides synchronized movement performance in high precision.
WORKPIECE SPECIFICATIONS | GBC-3210 | GBG-3210 |
---|---|---|
Max. workpiece outside diameter | 100mm | 100mm |
Max. module | M3 | M3 |
MECHANICAL SPECIFICATIONS | ||
Tool/grinding wheel spindle revolutions | 4000rpm | 12000rpm |
Max. slide travel for X-axis | 400mm | 400mm |
Max. slide travel for Y-axis | 350mm | 350mm |
Max. slide travel for Z-axis | 350mm | 350mm |
B- axis tilt range | -100°~100° | -100°~100° |
Smallest tool/wheel diameter | 0.5” | 0.5” |
Largest tool/wheel diameter | 4” | 4” |
Max. load of rotary table (workpiece with fixture) | 50kg | 50kg |
N-axis | Grinding spindle |
---|---|
X-axis | Tool horizontal movement axis |
Y-axis | Tool horizontal movement axis |
Z-axis | Tool vertical movement axis |
B-axis | Workpiece tilt axis |
C-axis | Workpiece rotation axis |
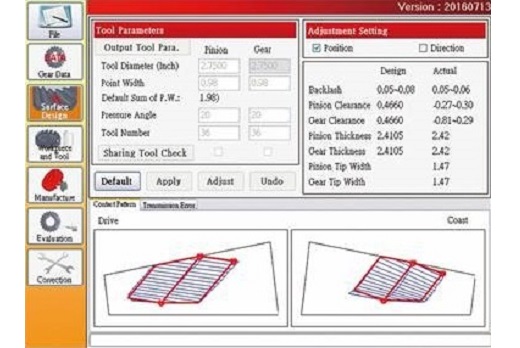
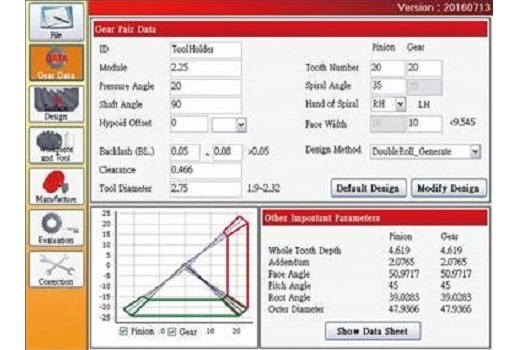
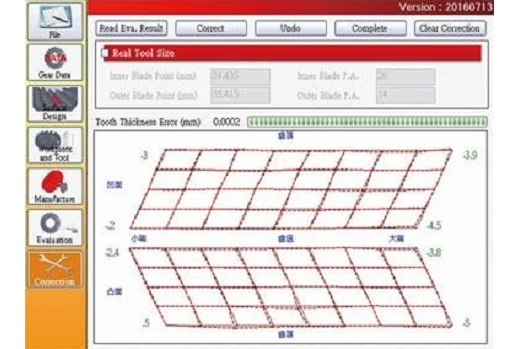
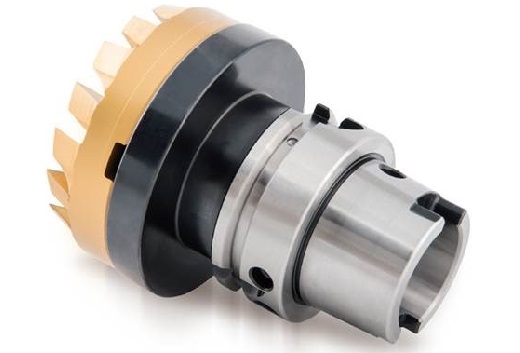